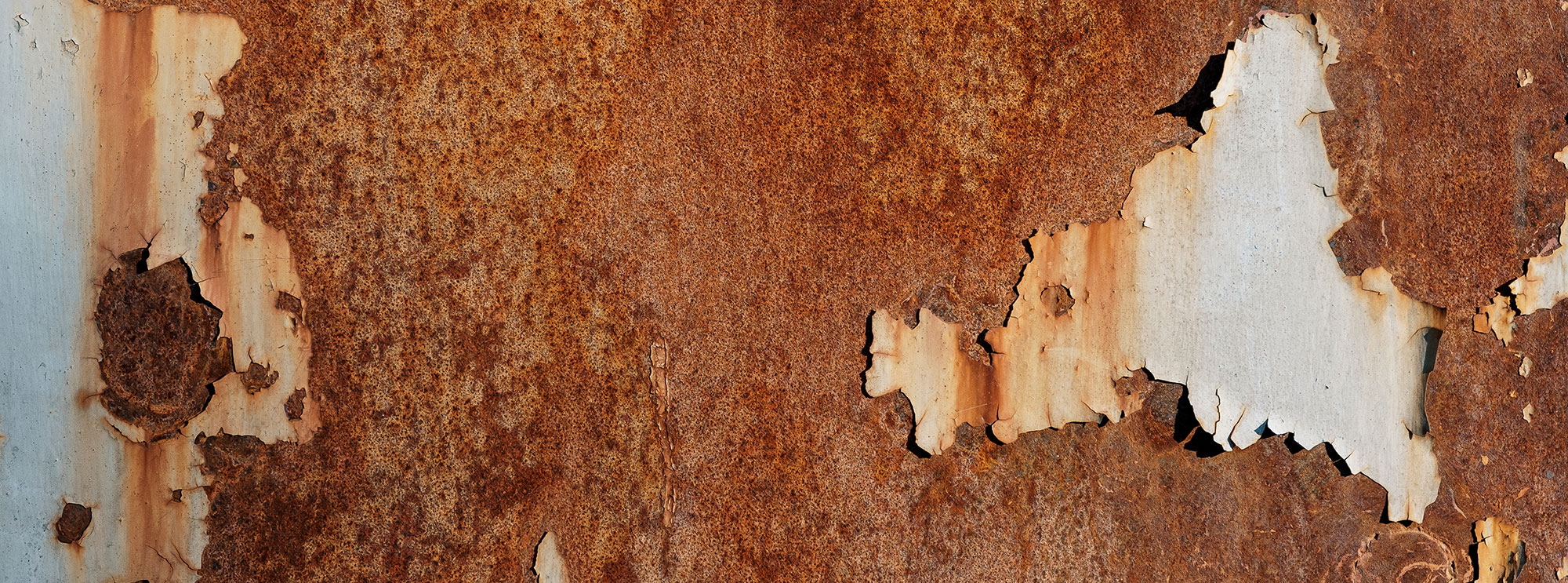
Condition? Satisfactory. That’s the rating for almost half of all German highway overpasses in 2023. A quarter of them ended up merely rated “Sufficient,” and just under five percent were not even that. There are many causes – moisture, fluctuating temperatures, mechanical stress. To find out what environmental influences affect an object and may cause it to deteriorate, researchers from Friedrich- Alexander-Universität Erlangen-Nürnberg (FAU) and the Fraunhofer Institute for Silicate Research ISC are pursuing a new approach in the SmartRust project.
Magnetic particles are incorporated into materials during the manufacturing process. Since these particles consist largely of iron oxides – rust, in other words – they are cheap to produce. They are also the namesake of the SmartRust project, which is receiving funding from the EU under a prestigious ERC Consolidator Grant. The particles are to provide information on what has happened to materials in the past, thereby bringing even hidden defects to light. “How much moisture has an object been exposed to? What about heat? Has it undergone mechanical stress? The idea is for the particles to answer questions like these for us, like tiny spies,” explains Karl Mandel, a professor of inorganic chemistry at FAU and deputy institute director and scientific director at Fraunhofer ISC.
The magnetic particles enable communication with the outside world. “When the particles interact with each other, it can be measured as a signal. You could almost say they’re whispering to each other – like little kids with a secret,” says Mandel, the project’s initiator. To be able to measure environmental influences, the researchers also plan to incorporate non-magnetic particles into materials; together with the magnetic particles, they form what is called a “supraparticle.” The non-magnetic particles react to specific environmental influences, such as salt, which dissolves in the presence of moisture. The supraparticle also changes when exposed to these external influences – so its “whispers” change in tone. A portable sensor can be used to register the difference in signal. Then, with the right kind of decoding, researchers can find out what has happened to the object.
Even through the sealed packaging of a vaccine, it would be possible to tell whether the cold chain had been interrupted, damaging the contents. In the automotive industry, people could find out whether plastic components had been heated to the specified temperature to form a sufficiently firm adhesive bond. Dangerous cracks in the blades of a windmill could also be detected and repaired early on. “The particles could let us see all the way into the invisible depths of an object – quickly, cheaply, and without destroying it,” Mandel explains. Once the technology is in use, he says it could be used for three main fields in the future. First is predictive maintenance, which brings greater product safety. Second would be greater efficiency in recycling, as it would enable reliable determinations of whether plastic still possesses the desired properties. And the last is more control in Industry 4.0, as objects could give robots feedback on aspects such as whether screws or bolts are actually placed correctly. Mandel is optimistic: “I’m fascinated by the idea of giving materials a voice down the road.”