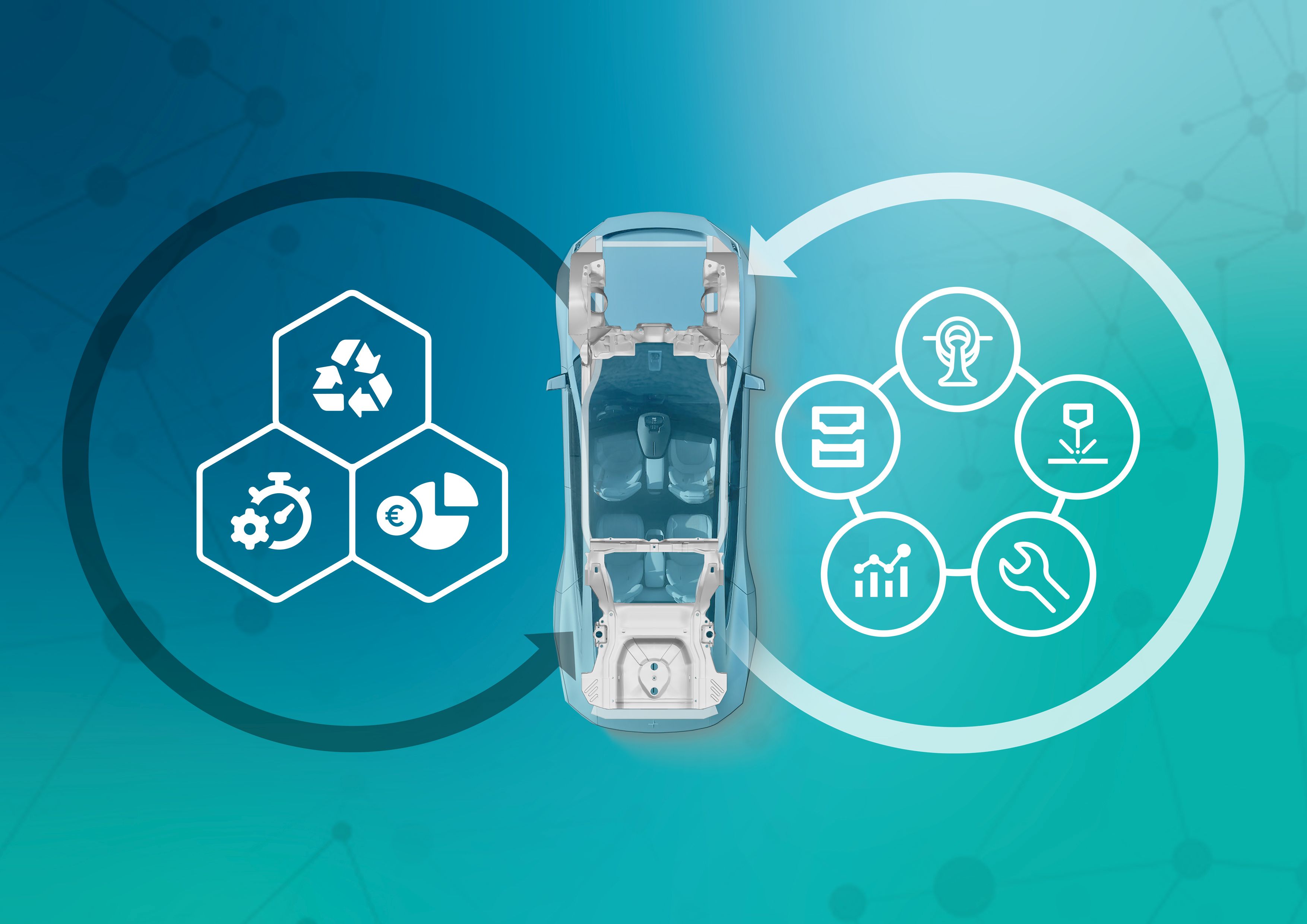
The automotive industry is currently undergoing the greatest transformation in its history. The transformation to electromobility an important building block in achieving climate-neutral mobility by 2050, as stipulated by the EU's Zero Pollution Action plan. Whereas, so far, around 80% of CO2 emissions have been caused by exhaust gases in the use phase, with electromobility, the CO2 hotspot is shifting from the use phase to the production phase. After the battery, the car body is the second largest emission driver and thus in focus to achieve environmental sustainability. It is expected that proof of sustainability will become the determining success factor for new body concepts.
The consortium behind the Future Car Production project aims to develop comprehensive approaches to assess new car body concepts in the automotive industry. To this end, methods, processes and technologies must be established to methodically evaluate and technologically guarantee ecological sustainability while meeting the conflicting priorities of technical performance and costs.
FutureCarProduction is thus responding to Tesla's new “giga-casting” concept, which challenges globally established design and production methods for car body construction. In this new method, highly integrated large castings are cast in one piece from aluminum, replacing entire body segments that were previously joined from many individual sheets and components. The Fraunhofer consortium’s approach using comprehensive sustainability analysis will also take into account optimizations in material and product quality, repairability and crash safety.