Reusing fiber composites in electric cars for up to 30 extra years
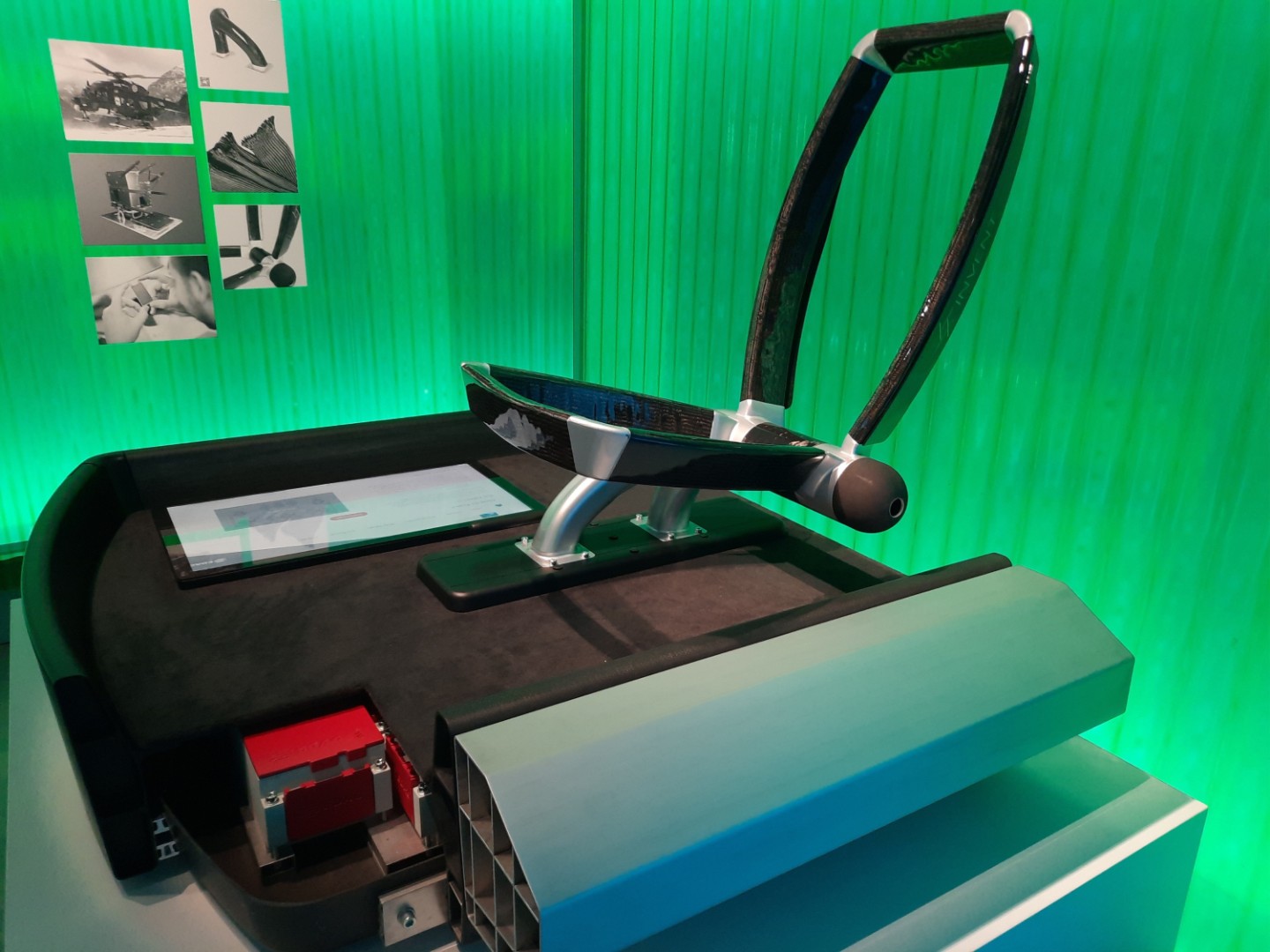
Many industries, including the aviation industry, are turning to carbon fiber-reinforced plastics (CFRP) to an ever greater extent. However, the advantages of these composites, like their low weight, come with disadvantages such as high manufacturing costs and limited recyclability. Until now, the costly components have mostly been disposed of as landfill or incinerated. New technologies and product ideas for fiber composite materials are now paving the way for economically viable reuse. These have been developed as part of the EU project “FiberEUse”. The project has involved 20 partners from seven countries, including the Fraunhofer Institute for Machine Tools and Forming Technology IWU.
One of the developments is a reusable platform for electric vehicles. The individual parts are designed to be usable for up to another 30 years after a car’s first service life. This applies not only to the vehicle frame, but also to the associated seating structure. The platform consists of extruded elements containing carbon fiber-reinforced plastic — these significantly improve the vehicle’s rigidity and protect the batteries from the impacts of any accidents. The longer period of use makes up for the high production costs.
To ensure that the platform and seating structure are durable, recyclable products, large yet simple profiles and nodal elements were combined with complex geometry. Technologies such as pultrusion, presses and detachable joining technologies are used in the production process. In most cases, fiber-reinforced plastics are adhesively bonded, so it is advisable to add thermally expandable particles to the adhesive for subsequent separation. After separation, the adhesive residues can be removed by a laser or by milling, for example, and the components can be bonded again.
The experts at Fraunhofer IWU firmly believe that the circular economy approach will generate new business models, especially in the automotive sector. They are developing new value creation cycles and business scenarios that will enable them to manufacture new products from recyclates.