Sensor systems with tiny micro-batteries to combat bee mortality
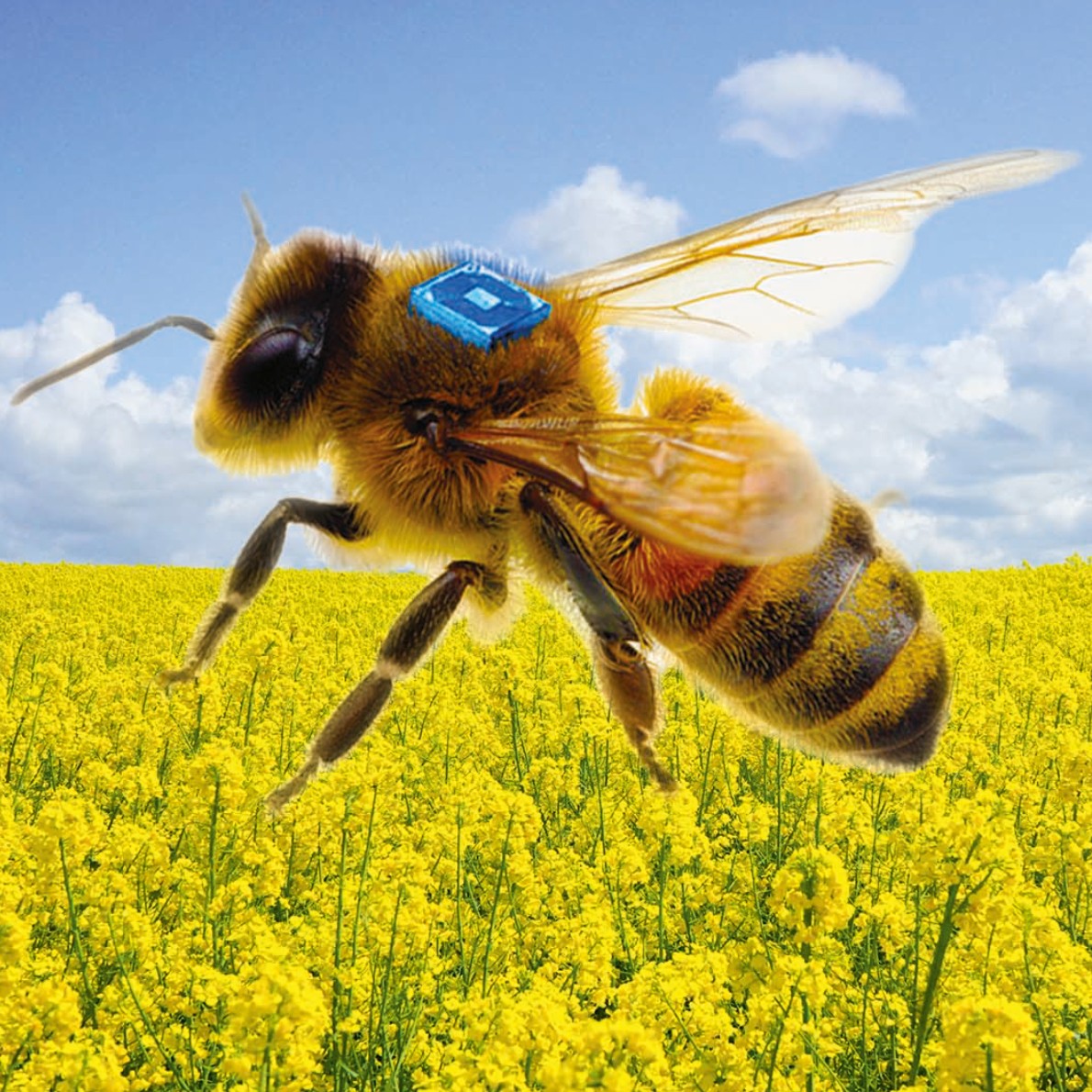
Bees do more than just provide us with honey; they also ensure the preservation of species by pollinating herbs, shrubs and trees. As a result, honeybees and wild bees generate about 1.6 billion euros for agriculture and food production in Germany, according to a study by the University of Hohenheim. With funding from the German Federal Ministry of Food and Agriculture (BMEL), the consortium of the “Sens4Bee” project is studying bee health against the backdrop of environmental and agricultural monitoring. Among other things, this involves fitting bees with a miniaturized, integrated sensor system in order to investigate the causes of global bee mortality.
Various sensor systems will be included to record parameters such as temperature, humidity, vibration, flight movement, brightness and acoustic signals in the hive and on individual bees. The data acquired will then be analyzed alongside environmental events and parameters. To this end, Micro-Sensys GmbH and the Fraunhofer Institute for Reliability and Microintegration IZM are developing sensors that combine an extremely small micro-battery and micro-energy harvesting in a single system. The resulting module needs to be so small and light (weighing less than 10 milligrams) that it can be carried by bees on their backs after being attached in an animal-friendly manner using a biocompatible adhesive. A miniaturized lithium battery, a solar module and tiny sensor data loggers will be integrated into the module. The battery is to be charged by daylight when the bees are out flying and by infrared light in the hive.
The data collected will be processed by the Helmholtz Centre for Environmental Research (UFZ), supplemented with environmental event data and analyzed in an intelligent cloud solution. The ultimate goal is to create a smart data processing system with recommended actions for beekeepers. Other partners involved in the project are the Julius Kühn Institute, Heinrich Holtermann KG and the German Beekeepers’ Association.